‘절삭’에 대응하는 것이 CMP이며 ‘프레스’에 대응하는 것이 나노임프린트이다. 나노임프린트 기술은 기존 CD나 DVD 제조에 사용되고 있는 서브마이크로미터 수준의 핫 엠보스(Hot Emboss) 기술과 기본적으로는 같은 기술이며, 다른 점은 1995년에 프린스턴대학의 슈(Chou) 교수가 프레스 기술은 몰드 표면원자가 전사(轉寫) 기판 위의 고분자 재료를 분자 수준으로 변위시킨다고 생각하고 실제로 10nm의 몰드를 제작해 고분해능 레지스트로서 알려져 있는 PMMA를 전사재료로 이용한 점이다.
이 성공 사례에서 배울 수 있는 점은 당연히 ‘나노테크놀로지는 원자·분자 수준에서 사색 창조하는 것’이라는 점이다. 또한, 미크론 사이즈의 기계가공기술이야말로 ‘나노테크놀로지’, 즉 고정관념을 타파한 발상의 ‘점프’가 중요하다. 나노임프린트의 출현은 연속적 사고·연구개발과 함께 불연속적 사고와 고정관념의 타파가 차세대 기술·제품을 창출해 간다는 것을 나타내고 있다. CMP, 나노임프린트 모두 지금까지의 정밀기계가공을 베이스로 단순한 발상에서부터 발전시킨 ‘원자론적 생산기술’이다.
당초 나노임프린트 기술이 발표됐을 때는 고정밀 프레스 장치를 사용해도 몰드와 전사기판의 평행을 맞추기 어렵다는 평가가 일반적이었다. 2000년에 슈 교수를 방문해 나노임프린트 장치를 견학했는데 얼핏 보기에는 그냥 일반적인 유압식 프레스였다. 일반적인 유압 프레스기와 다른 점은 기반의 초평활 연마기술과 평행 잡기 정밀기계기술이다. CMP와 나노임프린트 모두 어려운 사이언스를 바탕으로 개발된 것이 아니라 가공 사이즈를 원자 수준으로 생각한 단순한 아이디어를 실행에 옮긴 것이 성공의 열쇠이다. 이번 원고에서는 나노임프린트의 역사, 프로세스, 응용에 대해서 개설하고자 한다.
나노임프린트는 요철의 패턴을 형성한 몰드를 기판상의 액상 폴리머 등으로 눌러 패턴을 전사하는 것이다. 그림 1은 미세가공기술에 있어 나노임프린트의 위치를 나타낸 것이다. 10
nm 수준의 나노 구조체를 저렴한 가격으로 대량 생산할 수 있으며, 동시에 고정밀화가 가능함으로써 최근 주목을 받고 있다. 1995년에 슈 교수가 폴리머의 유리 전이온도 부근에서 승온과 냉각 과정에 의해 10nm 패턴 전사가 가능한 나노임프린트 기술을 발표했다. 열 사이클 프로세스이기 때문에 열나노임프린트라고도 불린다. 그 후 네덜란드의 필립스연구소(1996년), 미국 텍사스대학의 윌슨(Wilson) 교수가 자외광 경화수지를 이용한 빛(UV) 나노임프린트 기술을 발표했다. 그 후 전 세계 연구기관에서 나노임프린트 기술연구 개발이 시작됐고 10nm 패턴 전사가 가능한 것이 그 재현성과 함께 보고됐다.
또한, 나노임프린트 장치가 시판됨과 동시에 나노임프린트 기술이 일반화됐으며 그 응용 디바이스가 발표되게 됐다. 응용분야로서 얼라이먼트가 필요 없는 광학부품, 패턴드 미디어, 마이크로 유체 디바이스, 바이오 칩 등과 같은 디바이스 응용 연구가 이뤄지고 있다. 고정밀 얼라이먼트가 필요한 LSI 응용은 아직 연구단계이지만 IT·일렉트로닉스, 바이오·라이프 사이언스, 환경·에너지 모든 분야에서 나노임프린트 기술을 이용한 제품이 전개되고 있다고 해도 과언이 아닌 것이 현재 상황이다.
그림 2는 NNT2012 나노임프린트 국제회의(2012년 10월 24∼26일 미국 Napa에서 개최)에서 스웨덴의 룬드대학교 몬텔리우스(Montelius) 교수가 발표한 1995년부터 2011년까지의 나노임프린트 지역별 논문수(그림 2(a)), 지역별 특허수(그림 2(b)), 분야별 논문수(그림 2(c))를 나타낸 것이다. 지역별 논문수를 보면 나노임프린트 기술이 보고된 1995년부터 2000년 초까지 5년간은 논문수가 적다. 이것은 2000년까지 나노임프린트 장치가 시판되지 않았기 때문이다.
2006∼2011년의 지역별 논문수를 보면 아시아가 유럽 및 북미와 비교해 약 1.5배의 논문수를 나타내고 있다. 이는 액정 모니터의 반사방지막이나 LED 고휘도화를 위한 포토닉 결정 형성 등의 광학부품 응용 실용화 연구기에 들어가 이 디바이스를 생산하고 있는 일본, 한국, 대만에서 논문수가 늘어났기 때문이다. 지역별 특허수를 살펴보면 1995∼2000년(적다), 2001∼2005년(증가), 2006∼2011년(대폭 증가)로 지역별 논문수와 같은 경향을 나타내고 있다. 아시아와 북미의 특허수가 거의 같으며 유럽이 상대적으로 적다. 이것은 아시아 및 북미에서는 나노임프린트 연구가 기업 중심으로 이뤄지고 있는데 반해 유럽에서는 대학 및 공적 연구기관이 중심이 되고 있기 때문이다.
분야별 논문수를 보면 광나노임프린트가 열나노임프린트보다 2.7배 많은 논문수를 나타내고 있다. 나노임프린트의 연구 초기는 기본재료 그 자체를 가공하는 열나노임프린트가 주로 연구됐다. 그러나 나노임프린트의 응용 디바이스로서 반사방지막, 마이크로렌즈 등과 같은 광학부품, LED 고휘도화를 위한 포토닉 결정 제작 등 광학 디바이스를 응용한 연구가 왕성해져 프로세스 시간이 짧고 위치 맞춤이 가능한 광나노임프린트가 현재는 주류가 되고 있다. 스텝&플래시 나노임프린트는 미국의 몰큘로 임프린트사의 상표로 잉크젯을 이용해 광경화 수지 방울을 떨어뜨려 스텝&리피트하는 프로세스이다.
최근에는 제트&플래시라고 이름을 변경했다. 이 프로세스는 반도체나 패턴드 미디어 제조 프로세스로서 개발됐다. 스텝&리피트는 기본적으로 광나노임프린트에서 이용된다. 웨이퍼 일괄 전사는 열 및 광나노임프린트 양쪽 모두에서 이용할 수 있다. 디바이스를 살펴보면 LED 및 바이오 응용에 관한 논문수가 많다. GaN LED의 고효율화를 달성하기 위해서 고품질 GaN 에피택셜막을 사파이어 기판 위에 형성하기 위한 미세구멍 형성 및 외부 취출 효율을 증대시키기 위한 포토닉 결정 제작의 실용화에 관한 연구개발이 활발하게 이뤄지고 있기 때문이다.
바이오 응용으로서 세포 증식용 수지 필러 등의 광범위한 연구가 이뤄지고 있으며, 기초 연구와 함께 실용화 연구도 스타트된 단계다. 마이크로 유로 및 랩온어칩에서는 바이오센서, DNA 질량 분별 등의 기초 연구가 이뤄지고 있다. 태양전지에서는 태양을 효율적으로 흡수하기 위한 반사 방지 구조 형성, 패턴드 미디어에서는 고밀도 자기기록을 달성하기 위해서 피치 20nm수준의 패터닝 연구가 광나노임프린트를 이용해서 이뤄지고 있다.
MEMS/NEMS 응용은 센서 응용 관련인데 광학 및 바이오 응용에 비하면 연구논문이 적다. 나노임프린트는 콘택트 프로세스이기 때문에 결함 발생 및 양산 이형을 극복해야 하는 기술적 과제가 있다. 광학 디바이스 응용에 대해서는 어느 정도의 결함이 허용되기 때문에 현재 광학 디바이스에의 산업응용이 주로 이뤄지고 있다. 최근에는 메타 머티리얼, 플라즈모닉스에 대한 연구 발표가 증가하고 있다. 양산 이형에 대해서는 이형제와 함께 이형하기 쉬운 수지가 개발돼 점점 개선되고 있다. 광학 디바이스 다음에 올 실제 디바이스 응용으로서 기대되는 것이 유기 EL 등과 같은 플렉시블 일렉트로닉스, 태양전지, 연료전지 등의 환경 에너지 디바이스이다. 패턴드 미디어 및 LSI 응용에 대해서는 결함의 문제가 있어 기술적 장벽이 높지만 연구개발이 계속적으로 진행되고 있어 몇 년 이내에는 실용화의 실마리가 보일 것으로 기대된다.
나노임프린트 프로세스
열나노임프린트 기술
슈 교수팀에 의한 나노임프린트에서는 열가소성 수지인 PMMA(폴리에틸렌 메타크릴산 메틸 : 유리 전이온도(Tg) 105℃)를 기판에 도포하고 PMMA 폴리머층의 유리 전이온도 이상으로 승온해서 폴리머를 액상으로 만든다. 그 후 몰드(Ni 기판, Si 기판 또는 SiO2/Si기판의 SiO2층에 패턴 형성)를 프레스하고 유리 전이온도 이하로 냉각 후 몰드와 기판을 분리한다. 이 방식이 열나노임프린트이다. 전사 패턴을 제작하는 프로세스를 그림 3(a)에 나타낸다. 그 과정은 다음과 같다.
- 실리콘 기판에 열가소성 수지(PMMA 등) 박막을 도포한다.
- 열가소성 수지를 도포한 기판을 유리 전이온도보다 십 수 ℃ 높은 온도(PMMA의 경우 유리 전이온도가 105℃이므로 120∼150℃)까지 가열해 열가소성 수지를 연화시킨다.
- 몰드를 열가소성 수지에 접촉시키고 5∼10MPa로 가압해 레지스트를 변형시킨다.
- 프레스한 상태를 유지하면서 기판 온도를 냉각하고 수지를 경화시켜 몰드의 요철을 수지에 전사한다.
- 수지가 충분히 경화되면 몰드를 분리한다. 이 때 몰드의 볼록 부분에 상당하는 부분이 실리콘 기판 위에 얇은 잔막으로 남는다. 산소의 반응성 이온 에칭으로 잔막의 레지스트를 제거해 기판 표면을 나오게 한다. 이러한 슈 교수팀의 실험에 의해 10nm 이하의 전사가 가능하다는 것이 시사됐으며, 이번 기술 자체에는 해상도의 한계가 없고 해상도는 몰드의 제작 정밀도에 의해 결정된다는 것이 실증됐다. 현재의 포토마스크와 마찬가지로 몰드만 입수할 수 있으면 종전의 포토리소그래피로부터 간편하고 더 저렴한 장치로 극미소 미세구조를 형성할 수 있다. 그림 4는 Si 기판 위의 SiO2/Si 몰드를 이용해 열나노임프린트 된 10nm의 PMMA 전사 패턴을 나타낸 것이다. 또한, 사파이어 기판의 0.2nm 스텝을 유리 위에 전사한 열나노임프린트가 보고돼 있다. 이상과 같이 열 사이클 임프린트는 간편한 장치이며 대면적으로 10nm 오더 구조를 형성할 수 있는 양산기술로서 그 가능성을 가지고 있다.
광(UV)나노임프린트 기술
UV 나노임프린트는 실온 프로세스에서 석영기판 표면에 패턴의 요철을 붙인 투명 몰드를 이용한다. 저점성 광경화 수지를 레지스트로 이용하기 때문에 석영 몰드의 레지스트에 대한 프레스압은 열나노임프린트가 5∼10MPa인데 대해서 0.1MPa 이하로 대단히 작다. 이 특징들 때문에 위치 맞춤 정밀도 및 중합 정밀도는 기본적으로 현상의 빛 스탭퍼(Stepper)와 동등한 정도라고 기대할 수 있다. 패턴 전사에는 자외광이 이용되는데 그 해상도는 빛의 파장에 의존하지 않고 석영 몰드의 패턴 사이즈에 따라 결정된다. 이 프로세스를 그림 3(b)에 나타낸다. 이 프로세스는 다음과 같은 과정을 거친다.
- 실리콘 기판 위에 광경화 수지 박막을 도포 형성한다.
- 실온에서 점도가 낮은 광경화 수지를 석영 몰드로 변형시킨다.
- 자외광(300∼400nm : 통상 365nm)
을 조사해서 수지를 경화시킨다.
- 몰드를 분리해 패턴을 얻는다.
패턴을 얻기 위해 자외광만 조사하면 되므로 열 사이클에 비해 스루풋(Throughput)이 높으며 온도에 의한 치수변화 등을 막을 수 있다. 또한, 몰드에는 자외광을 투과하는 몰드를 사용하므로 몰드를 투과하고 난 뒤의 위치 맞춤을 할 수 있다는 이점도 있다. 스텝&리피트에 의해 웨이퍼 전면에의 임프린트도 가능해진다. 광나노임프린트용 몰드로서 석영이 사용된다.
LER(Line Edge Roughness)가 0.6nm인 몰드를 이용해 UV 나노임프린트용 광경화 수지 PAK-01(도요고세이사)에 전사한 결과 전사 패턴의 LER은 0.8nm이라는 결과가 나와 광나노임프린트의 낮은 LER 전사 특성이 실증됐다. 또, 선폭 5nm의 석영 나노임프린트 몰드를 전자 빔 노광과 드라이 에칭으로 제작하여 UV 나노임프린트한 결과 그림 5에 나타낸 것과 같이 최소 선폭 5nm 패턴의 전사에 성공했다. 또, 지름 2.4nm의 카본 나노 튜브를 PDMS로 형을 만들어 PDMS 몰드를 이용해서 UV 나노임프린트해 선폭 2.4nm의 광경화 수지 패턴을 전사한 것이 보고되어 있다.
나노임프린트의 적용 상황
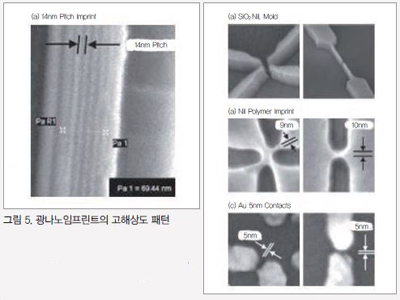
그림 6은 NEDO에 의해 작성된 나노임프린트 로드맵으로 IT, 환경·에너지·바이오 산업진흥에 불가결한 핵심 테크놀로지로서 자리매김하고 있다. 국내외에서 나노임프린트 기술의 산업화가 현실이 되어 가고 있는 상황 속에 나노임프린트 장치, 전사 재료·몰드·이형재 등과 같은 나노임프린트 부품으로의 기업 진출이 잇따르고 있으며 나노임프린트 연구개발·비즈니스가 급속도로 전개되고 있다. 나노임프린트의 응용분야는 먼저 LCD의 플랫 패널 디스플레이에 있어 도광판, 무반사방지막, 금속 와이어 편광판 등의 광학부품, 마이크로렌즈 어레이, 광도파로 등의 광학부품, 연료전지, 태양전지 등의 에너지 디바이스, 바이오 디바이스 등에서 응용 연구개발이 진행되고 있다.
디스플레이 부품
나노임프린트가 양산기술로서 적용 전개되고 있는 것은 면적이 몇 cm부터 m 오더까지에 걸쳐 있는 휴대전화부터 액정 TV의 플랫 패널 디스플레이(FPD) 부품 응용부문이다. 도광판, 반사방지막, 편광판 등의 광학부품 생산에 나노임프린트가 적용되고 있다. 도광판은 프레넬 렌즈(Fresnel Lens) 구조 등과 같은 미크론 오더의 삼차원 구조이다. 지금까지 사출성형으로 제조되고 있었는데 고효율 도광판을 제조하기 위해서는 고정밀 삼차원 구조 제조가 중요해 사출성형으로는 필요한 삼차원 구조를 고정밀도로 충전할 수 없게 됐다. 그 때문에 사출성형을 대신해 나노임프린트 기술이 제조라인에 점점 전개되고 있다.
주기 100nm의 고효율 금속 와이어 편광판에 대해서는 아사히카세이가 나노임프린트를 이용해서 제품을 전개하고 있다. 또, 소니는 플랫 패널 디스플레이용의 반사 방지 필름의 원판이 되는 몰드를 Blu-ray 제조기술을 이용해 단시간에 제조하는 기술을 확립하고 통상 제조 프로세스보다 고성능인 0.1% 이하의 반사 방지 필름 제조에 성공했다. 또한, 샤프는 100nm 주기의 모스아이 구조를 가진 60인치 사이즈의 반사방지막을 제조해 LCD 텔레비전에 실제 탑재해 고성능을 입증했다. 이상에 나타낸 것과 같이 이미 나노임프린트는 디스플레이 부품 응용에 불가결한 제조기술로서 전개되고 있으며 대면적 대응 고속 나노임프린트 기술로서 롤러 나노임프린트의 제조가 전개되고 있다.
광학부품
마이크로렌즈 등의 광학부품 제조에는 지금까지 사출성형을 이용해 왔지만 고정밀 마이크로렌즈 제조에의 대응이 곤란해 나노임프린트 기술이 고정밀 마이크로렌즈 제조에 이용되고 있다. 마이크로 렌즈 어레이는 디지털 카메라, 휴대용 카메라에 탑재되고 있어 대형 시장 전개를 예상할 수 있다. 또한, 광도파로 제조에서도 고정밀 가공이 가능하기 때문에 손실이 적어 나노임프린트 기술이 도입되고 있다.
LED, 태양전지에의 응용
GaN 표면에 구멍 지름 100nm 수준의 주기 구조를 가지는 포토닉 결정구조를 나노임프린트로 형성하는 것으로 빛의 지향성 향상과 함께 취출 효율이 1.5배가 됐고 GaN의 LED 고효율화가 실현돼 이미 시장에 전개되고 있다. 또, 태양전지에서는 실리콘 태양전지의 유리 보호막 투과율을 향상시켜 발전 효율을 증대시키기 위해서 유리 보호막의 한 면 또는 양면에 나노임프린트로 300nm 주기의 모스 아이 구조를 형성했다. 연료전지에 대해서도 나노임프린트로 격벽막의 면적을 증대시켜 효율 향상을 도모하는 연구개발이 이뤄지고 있다.
현재의 바이오 응용 시장은 광학부품 등에 비하면 크지 않지만 패턴 사이즈, 1회용 디바이스라고 하는 특징으로부터 나노임프린트 이용율의 성장을 기대할 수 있는 분야다. 바이오·의료 분야 등에의 응용 예로서 미소량의 액체를 제어하는 시스템인 마이크로 TAS(Micro Total Analysis System) 디바이스가 주목을 받고 있다. 유로(流路) 내에 제작된 작은 구조체에 의해 사이즈를 선별하는 DNA/Protein 바이오 칩, 고에스펙트 나노 구조를 가지고 있는 세포배양 시트 및 항원항체반응 검출 시트 등이 보고돼 있으며 시장 전개를 계획하고 있다.
패턴드 미디어
하드디스크 드라이브(HDD)는 현재 컴퓨터의 대용량 기록매체로서 중심적인 역할을 하고 있다. 1990년대에는 10년에 100배라고 하는 경이로운 신장율로 증대됐다. 그러나 2000년부터 성장이 둔화되고 있다. 이것은 안전하게 기록할 수 있는 자성체 도트의 최소 사이즈로 매체의 기록 단위가 근접해 가고 있는 것이 원인 중 하나이다. 1Tbit/inch2를 넘는 대용량 HDD용 고밀도기록 미디어에서는 인접 트랙 사이의 자성체를 물리적으로 분리하는 패턴드 미디어가 유력해 20nm 스케일의 주기 패턴을 미디어 전면에 제작하는 것이 필요하다. 이 때문에 하드 디스크의 패턴드 미디어에 있어서는 나노임프린트 기술이 필수적인 양산기술로서 연구 개발되고 있다.
반도체 응용
나노임프린트는 1995년의 슈 교수에 의해 제안됐고 1997년에 열나노임프린트에 의해 PMMA의 10nm 패턴이 제시된 시점부터 반도체 LSI에의 적용 가능성에 대해서 논의가 시작됐다. 나노임프린트 기술은 ITRS(International Technology Roadmap for Semiconductors) 로드맵 2011년판에서도 EUV 리소그래피와 함께 22nm 이후의 반도체 제조기술 후보로 올라 있다. 또한, 2011년에는 미국의 반도체 컨소시엄인 세미테크(SEMATECH)의 맷 말로(MattMalloy)와 로이드 C 리트(Lloyd C. Litt)에 의해 나노임프린트의 반도체 리소그래피 적용이 논의됐다.
나노임프린트의 반도체 LSI 프로세스에의 적용은 등배 전사이므로 몰드의 제작이 빛 노광 마스크의 4배체에 비해 어렵고 콘택트 프로세스이므로 결함이 발생하기 쉬운 등 해결해야 할 과제가 있어 당초에는 실용화가 어렵다고 생각됐다. 그러나 5nm 이하의 고해상도, 패턴의 엣지 러프니스가 몰드의 엣지 러프니스와 동일한 정도로서 몰드 제작 정밀도에 따라 실용화 가능성이 그리고 삼차원 몰드를 이용함으로써 Dual Damascene 프로세스 공정을 간소화할 수 있고, 장치가격이 저렴한 이점이 있어 연구개발이 진행됐다.
나노임프린트에 의한 첨단 반도체 제조장치를 개발하고 있는 벤처기업 몰큘러 임프린트사(MII)가 2001년 2월에 미국 텍사스주 오스틴시에 설립되어 장치개발이 적극적으로 실시됐다. 2014년 2월 5일에는 캐논이 모큘러 임프린트사와 연결 자회사화를 합의했으며, 캐논이 하프 피치 20nm 미만의 NAND 플래시 메모리 차세대 반도체 나노임프린트 노광장치를 반도체 제조사에 공급하고 있는 단계에 있다.
급속한 시장 성장세
나노임프린트 기술은 슈 교수의 발명으로부터 지금까지 20년간 장치개발, 프로세스 개발, 몰드·재료 개발 등이 세계적으로 활발하게 추진돼 디스플레이 부품, 광학 부품, 에너지 디바이스, 바이오 디바이스 등 패턴드 미디어 및 LSI 이외에의 양산 응용 전개가 빠른 속도로 진행되고 있다. 이미 마이크로렌즈, 반사방지막, LED 등에의 실제 디바이스 응용이 이뤄지고 있으며, 최근에는 에너지 분야로서 연료전지의 반응장 격벽이나 태양전지의 표면에 나노임프린트에 의해 요철을 만들어 효율을 높이고 있다. 이와 같이 나노임프린트 기술을 적용한 시장은 빠른 속도로 성장하고 있으며, 그 각 제품의 시장규모는 대단히 크다. 나노임프린트 기술을 가지고 제품을 전개함으로써 기업의 기술 차별화, 우위성을 도모할 수 있다. 가까운 장래에는 패턴드 미디어 및 LSI의 양산 적용 연구도 시작될 것으로 기대된다.
마쓰이 신지
효고현립대학
나노임프린트 연구개발센터 교수
SOLAR TODAY 편집국(st@infothe.com)
<저작권자 : 솔라투데이 (http://www.solartodaymag.com/) 무단전재-재배포금지>
저작권자 © 인더스트리뉴스 무단전재 및 재배포 금지